ABA Corp implements six cobots to run their CNC machines in their high mix production
"Since adding six robots, we haven’t let go of a single person. We’ve actually ramped up our workforce."

Background of ABA Corp's CNC machined parts
Rob Frankel and Kim Frankel, co-founders of ABACORP CNC Machined Parts, saw cobots as a tool to enhance operations. “When cobots were first introduced, we saw the potential for innovation and technology that could help us compete in the marketplace,” says CEO Kim Frankel.
Like Bogart, COO Rob Frankel entered the workforce at a young age. “I was 15, riding my bicycle and knocking on doors, looking for a job. A machine shop responded,” he recalls.
The work fit Frankel like a glove. He began honing other skills like welding and fabrication before eventually taking a job at Haas Automation, where he ran its application engineering department. As Frankel gained experience, he found he was hard-wired for the industry and began to think about running his own manufacturing company.
“Someone told me that if you ever want to buy equipment, putting a CNC machine in your hands is like printing money,” he says. “That got the ball rolling. Kim and I talked and decided to start ABACORP” in 1997 in Moorpark, California.
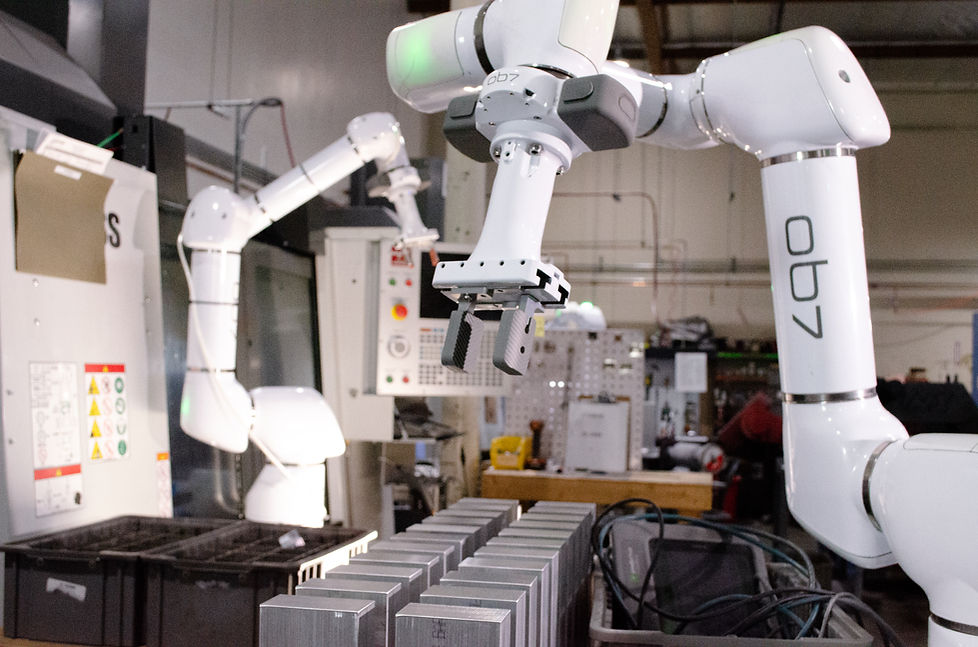
ABACORP serves automotive, aerospace, communications and electronics, medical devices, military and retail markets. Services include milling, turning, engineering, welding, assembly, total product solutions, and outside process finishing such as powder coating and anodizing. The AS9100 certified machine shop has a finished product first pass quality yield of 98.7 percent.
“When I saw robotics hit a price point that fit our budget, I decided to jump in and take advantage of the technology,” says Rob Frankel. “We were drawn to Productive Robotics because their cobots were locally built.”
The job shop installed its first two OB7 cobots in 2018. Today ABACORP has six OB7 cobots tending machines, loading and unloading parts.
New standard
“I’ve heard the argument that robots get rid of people,” says Frankel. “I disagree. Our cobots have been taught to perform the mundane tasks that permeate a traditional job shop. We’ve taken entry-level operators whose only job was to stand and tend a machine for minimum wage and retrained them to increase their responsibilities and their capabilities, experience and growth for a higher earning position. Since adding the robots, we haven’t let go of a single person. We’ve actually ramped up our workforce.”
In 2021, growth prompted ABACORP to move to a larger facility, expanding by 7,500 sq. ft. The job shop manages small to large production run orders. Each cobot picks up parts from a bench, loads and unloads them from a CNC machine tool and places them in a box. An operator inspects part features.
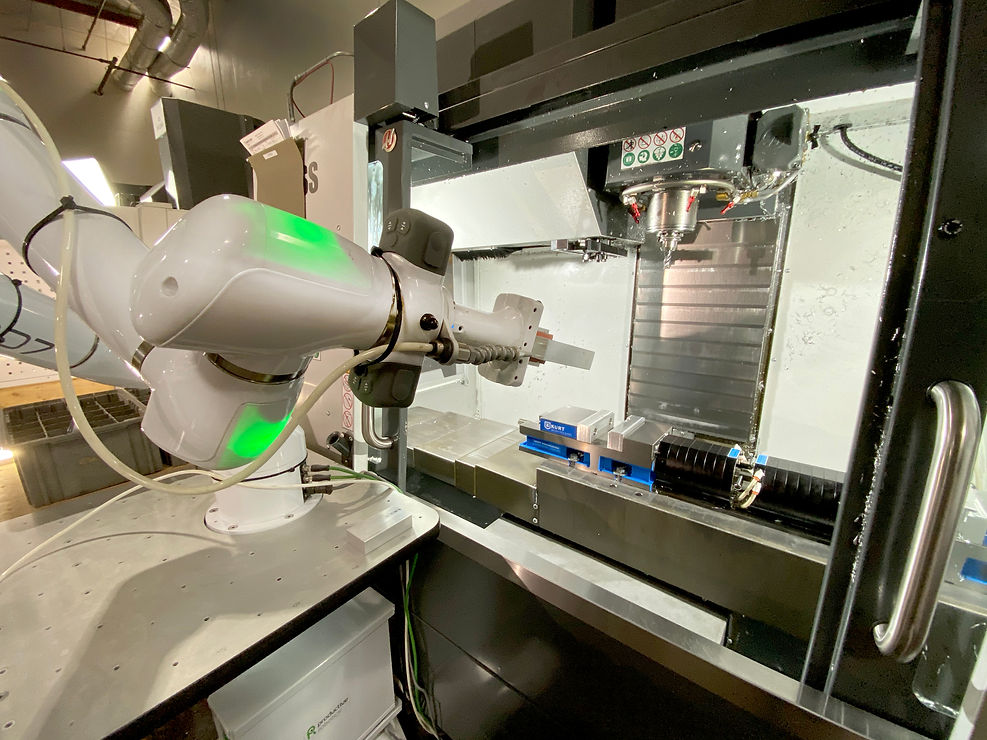
“It sounds simple,” says Frankel. “But I’ve seen a lot of parts loaded incorrectly by operators. Cleaning the vise, pushing the part against the back stop using the same technique each time are things that are easy to forget. The cobots are repeatable and consistent. When they load parts, they do it exactly the way we showed them to every time.”
Once the OB7 is taught what to do, the job is saved. “A two-hour setup job with the cobot can be reduced to 15 minutes on repeat jobs,” Frankel adds. “It already knows what to do. Even if you are only running 30 parts, you can boost throughput with the cobot.”
The AI “co-workers” are also helping create a healthier work environment. “Shop floor processes are repetitive by nature,” says Frankel. “People end up with wrist and finger conditions. I’ve run millions of parts myself.”
Frankel noted that contract shops using other cobot model brands on the market, have expressed surprise at ABACORP’s success with OB7. “One individual confided they had only used their robot a couple of times but experienced failure,” he says. “We didn’t have that problem. Productive Robotics helped us understand how to integrate the OB7 into our workflow.”
This is from an article that was featured in FF Journal Magazine. To read the full article, click here.